Tech
Hydraulic vs. Air Brakes in Mining: Comparing the Pros and Cons
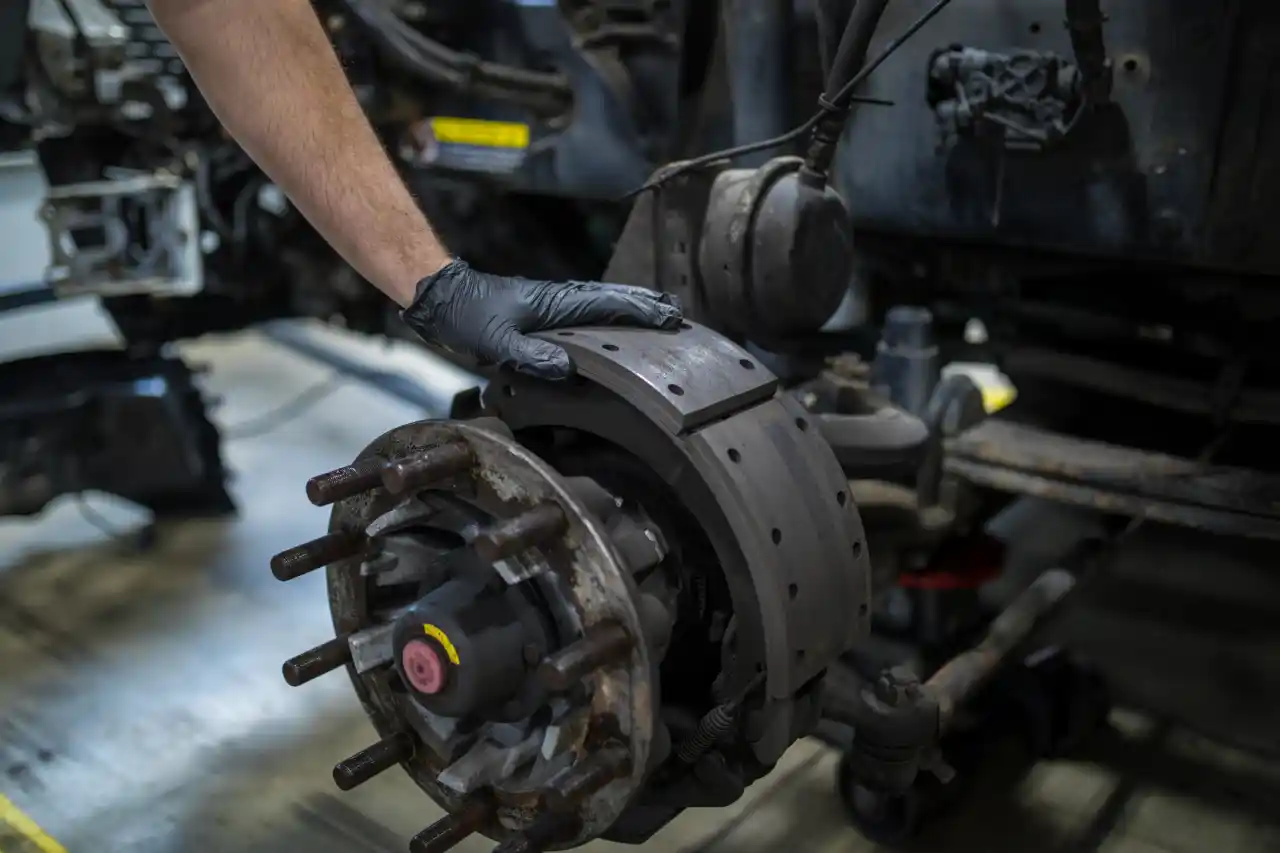
The Importance of Reliable Braking Systems in Mining
In the rugged world of mining, safety and efficiency are paramount. One of the most critical components of mining equipment is the braking system. Whether it’s massive haul trucks navigating steep grades or underground loaders maneuvering through tight spaces, the ability to stop safely and effectively is essential. This article compares two popular types of mining equipment brakes: hydraulic and air brakes, exploring their advantages and disadvantages.
Understanding Hydraulic Brakes
Hydraulic brakes use fluid pressure to transmit force from the brake pedal to the brake pads or shoes.
Advantages of Hydraulic Brakes
- Responsive and precise control
- Compact design, ideal for smaller equipment
- Lower maintenance requirements
- Quiet operation
Disadvantages of Hydraulic Brakes
- a) Limited effectiveness on larger, heavier vehicles
- b) Potential for fluid leaks
- c) Susceptibility to brake fade under extreme heat
- d) More complex bleeding and fluid replacement procedures
Exploring Air Brakes
Air brakes use compressed air to apply force to the brake pads or shoes.
Advantages of Air Brakes
- Excellent for heavy-duty applications
- Consistent performance in various conditions
- Easier to maintain and inspect
- Built-in fail-safe mechanisms
Disadvantages of Air Brakes
- Slower response time compared to hydraulic systems
- More components, increasing potential points of failure
- Noisier operation
- Requires regular drainage of air tanks to prevent moisture buildup
Factors Influencing Brake Choice in Mining
When selecting mining equipment brakes, several factors come into play:
Vehicle Size and Weight
- Hydraulic brakes: Suitable for smaller to medium-sized equipment
- Air brakes: Preferred for large, heavy-duty vehicles
Operating Environment
- a) Temperature extremes
- b) Dust and debris exposure
- c) Moisture levels
- d) Terrain conditions
Maintenance Requirements
- Hydraulic systems: Less frequent but more complex maintenance
- Air systems: Regular but simpler maintenance procedures
- Safety Considerations
- Fail-safe mechanisms
- Redundancy in braking systems
- Ease of inspection and troubleshooting
Hydraulic Brakes in Mining Applications
Hydraulic brakes find their niche in certain mining scenarios:
- Underground mining equipment where space is limited
- Precision control for delicate operations
- Vehicles operating in environments where air compressor noise is a concern
Air Brakes in Mining Applications
Air brakes excel in various mining situations:
- Surface mining with large haul trucks
- Equipment operating on steep grades
- Vehicles requiring frequent stops and starts
- Operations in extreme temperature conditions
Hybrid Systems: Combining Hydraulic and Air
Some mining equipment manufacturers are exploring hybrid braking systems that combine the strengths of both hydraulic and air brakes:
- Using air brakes for primary stopping power
- Incorporating hydraulic systems for fine control and emergency braking
- Balancing the benefits of both systems for optimal performance
Maintenance Considerations
Proper maintenance is key to ensuring the longevity and reliability of mining equipment brakes:
Hydraulic Brake Maintenance
- a) Regular fluid checks and replacements
- b) Inspection of hoses and fittings for leaks
- c) Brake pad wear monitoring
- d) Bleeding the system to remove air bubbles
Air Brake Maintenance
- Daily draining of air tanks
- Regular checks of air compressor function
- Inspection of air lines and fittings
- Adjustment of brake slack adjusters
Safety Features in Modern Braking Systems
Advancements in technology have led to improved safety features in mining equipment brakes:
- Anti-lock braking systems (ABS) for better control
- Electronic stability control integration
- Automated emergency braking systems
- Advanced monitoring and diagnostic capabilities
Environmental Considerations
The choice between hydraulic and air brakes can have environmental implications:
- Fluid disposal and potential leaks with hydraulic systems
- Energy consumption of air compressors in air brake systems
- Noise pollution considerations, especially in underground operations
- Longevity and recyclability of components
The Future of Mining Equipment Brakes
As mining technology evolves, so do braking systems:
- Integration of regenerative braking for energy recovery
- Development of more environmentally friendly brake fluids
- Advancements in materials for longer-lasting brake components
- Increased use of sensors and AI for predictive maintenance
Making the Right Choice for Your Mining Operation
Selecting between hydraulic and air brakes for mining equipment requires careful consideration of various factors:
- a) Analyze the specific requirements of your mining operation
- b) Consider the types of vehicles and their typical use cases
- c) Evaluate the operating environment and conditions
- d) Factor in maintenance capabilities and resources
- e) Consult with equipment manufacturers and brake specialists
The Importance of Training and Familiarity
Regardless of the braking system chosen, proper training is essential:
- Educate operators on the specifics of the braking system
- Conduct regular refresher courses on brake operation and maintenance
- Implement clear procedures for brake inspection and reporting issues
- Foster a culture of safety and proactive maintenance
Choosing between hydraulic and air brakes for mining equipment is not a one-size-fits-all decision. Each system has its strengths and weaknesses, and the best choice depends on the specific needs of your mining operation. By carefully considering factors such as vehicle size, operating environment, maintenance capabilities, and safety requirements, you can select the braking system that will provide the best performance, reliability, and safety for your mining equipment.
Remember, the effectiveness of any braking system relies not just on its design but also on proper maintenance, regular inspections, and skilled operation. Whether you opt for the responsive control of hydraulic brakes or the robust power of air brakes, ensuring that your mining equipment brakes are in top condition is essential for the safety and efficiency of your mining operations.